Regardless of the actual value of the products, you see the potential of using related ferroalloys in this section.
All content on this page has been created by ChatGPT 4 AI

Microsilica
Microsilica plays a crucial role in concrete production, exerting various effects such as enhancing strength and durability, increasing density, reducing water absorption and separation, minimizing thermal cracking, and offering environmental benefits.
Strength and Durability
Microsilica possesses pozzolanic properties, reacting with calcium hydroxide in cement to form additional calcium silicate hydrate (C-S-H) gel. This reaction leads to increased strength and durability of concrete by improving its compressive strength, enhancing resistance against chemical reactions, and reducing permeability.
Increase in Density
Due to its high specific surface area, Microsilica fills the voids between cement particles, resulting in a denser concrete matrix. This increase in density improves the mechanical properties of concrete, including its strength and resistance to wear.
Reduction in Water Absorption and Segregation
Microsilica acts as a filler in concrete, enhancing cohesion and reducing water absorption and segregation. This results in a more homogeneous and uniform concrete mix, reducing the risk of water separation and aggregate segregation.
Environmental Benefits
Incorporating Microsilica into concrete compositions helps reduce waste and decrease the carbon footprint associated with cement and concrete production. By using Microsilica, construction projects can contribute to sustainable practices and environmental conservation.
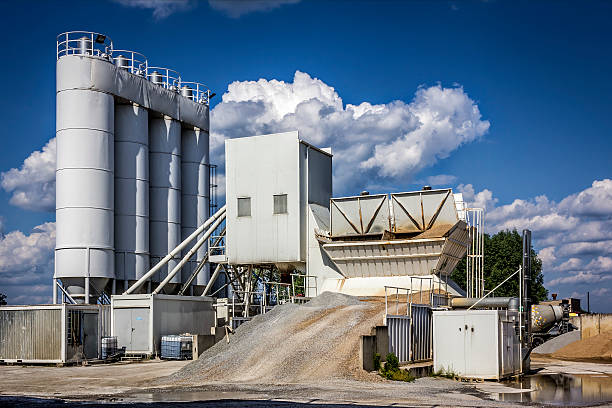
Reduction of Thermal Cracking
Microsilica’s presence in concrete reduces thermal cracking by improving thermal insulation properties and minimizing internal temperature gradients. This helps mitigate the risk of concrete cracking under high temperature conditions, enhancing its durability and longevity.
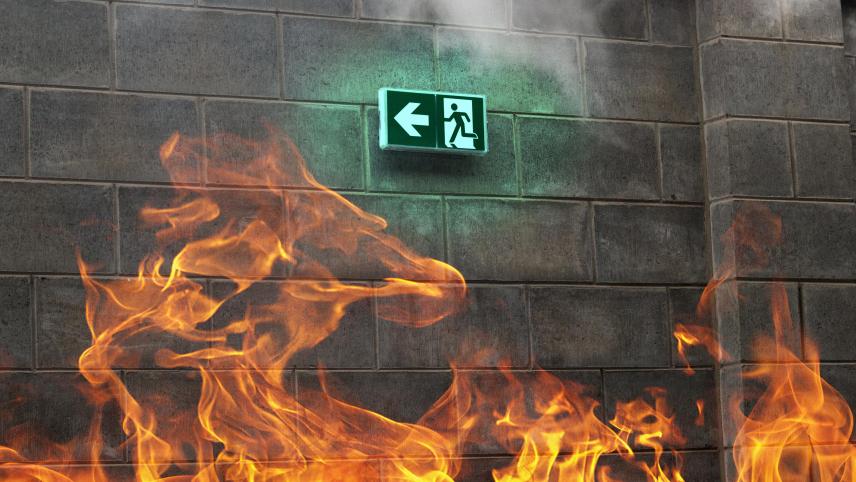
Grout
Ferrogel improves the mechanical properties and durability of concrete, enhancing adhesion, reducing water shedding, improving mechanical strength, reducing permeability, and increasing wear resistance.
Base Gel
Used to reduce cracking in concrete, especially in slabs, base gel improves durability and appearance, delays concrete setting time, reduces water-to-cement ratio, and enhances resistance properties.
Fibrous Base Gel
This type of gel, containing fibers made from polypropylene material, prevents shrinkage and paste cracks in concrete slabs, floors, and tops, enhancing durability and surface quality.
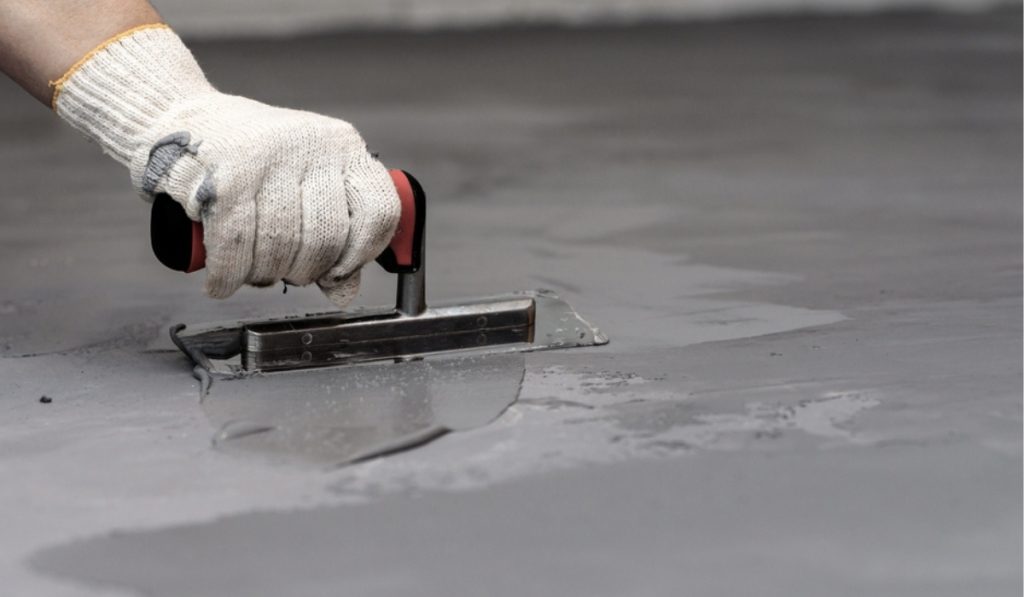
High Slump Fibrous Gel
Suitable for hot weather conditions, slump high fiber gel improves concrete surface quality in slabs and floors, reduces shrinkage and cracking, and maintains maximum slump.
High Slump Gel
Serving as a water reducer, high slump gel increases concrete fluidity without compromising properties, facilitating void filling during pouring.